MIG Welding
(Click to Expand)

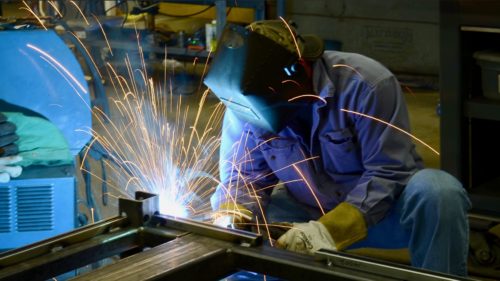
Metal inert gas (MIG) welding is technically referred to as gas metal arc welding (GMAW). As an arc welding method, it uses an electric arc to generate heat, which melts and joins the materials. The arc is created by feeding a continuous wire electrode through the welding gun and into the molten weld pool while a power supply applies electrical to it and the base material(s). The welding gun also supplies a shielding gas, which protects the welding from environmental contamination.
Compared to other welding techniques, the MIG welding process is simpler to learn and easier to perform. It is also one of the most versatile welding methods available and suitable for joining everything from thin sheets to thicker-section components. Its key advantages include:
- Short operation and low cost: The feed wire and other equipment required to perform MIG welding are readily available and relatively inexpensive. The process is also much faster to perform than TIG welding and other more advanced welding techniques.
- Broad material compatibility: The MIG welding process can be used to join many materials, including aluminum, carbon steel and stainless steel. Additionally, it can accommodate materials in various thicknesses.
- High weld quality: MIG welding offers a high level of control over the welding process, allowing for the formation of high-quality, long-lasting welds.
- Excellent versatility: The MIG welding process is highly adaptable. It lends itself well to both semi-automatic and high-speed robotic welding processes. It is also ideal for forming tack and spot welds.
Due to its many advantages, MIG welding is one of the most widely used welding methods. Typical applications include:
- Automotive assembly and repair
- Structural construction
- Sheet metal welding
TIG Welding
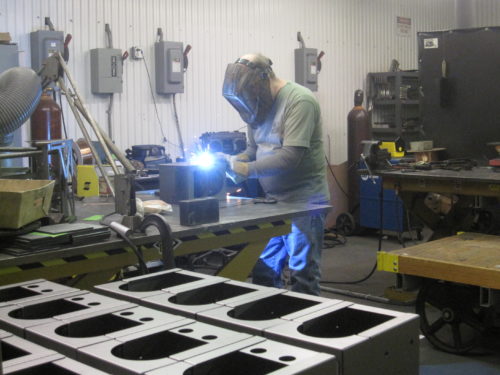
Tungsten inert gas (TIG) welding—also referred to as gas tungsten arc welding (GTAW)—is another arc welding method. It uses a fixed non-consumable tungsten electrode to create the arc that forms the weld pool. The arc heats the materials, allowing them to melt and fuse together. Similar to the MIG welding process, this process uses a shielding gas to protect the weld area from atmospheric contamination.
Compared with MIG welding, the TIG welding process is generally more time-consuming and requires a higher skill level to perform. However, it provides more accuracy and control over the welding process, which can facilitate the formation of a higher-quality weld. Its key advantages include:
- Clean welds: TIG welding is typically preferred for applications requiring an exceptionally smooth, aesthetically appealing weld between joined surfaces.
- Small, thin material suitability: Since the TIG welding process allows the welder to weld with a greater degree of accuracy, it is well-suited for joining small and/or thin materials.
- Broad versatility: The TIG welding process can be used to weld everything from standard steels to specialty stainless alloys. The welds can also be created in various positions, including vertical, horizontal, flat, and overhead.
The enhanced level of control offered by TIG welding makes it ideal for applications in which a clean, precise weld is critical to the quality and safety of the final product. For example, the highly regulated aerospace industry often relies on TIG welding for the construction of everything from commercial planes to complex spacecraft. Other applications of TIG welding include:
- Automobile parts
- Defense/military technologies
- Electronic enclosures
- Food manufacturing and packaging equipment
- Pharmaceutical manufacturing equipment
Laser Welding
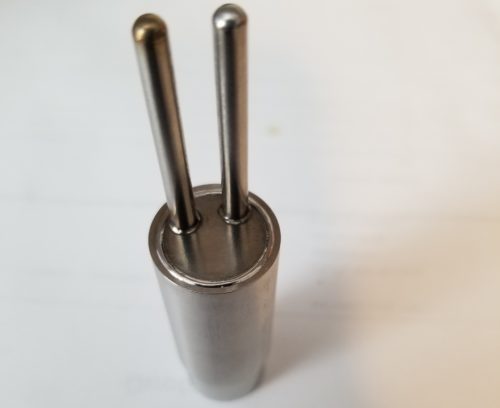
Laser welding, or Laser Beam Welding (LBW) is a fuse welding process in which two metal or plastic pieces are joined together by the use of a laser beam. The laser is a highly concentrated heat source that produces a clean, strong, ultra-precise weld with deep penetration and a small heat affected zone. The advantages of laser welding are:
- Ability to weld material that would be too thin for other methods.
- The small heat affected zone results in minimal thermal distortion
- Welds are cleaner than MIG or TIG minimizing the risk of contamination
- Most of the time there is no need for post-processing grinding or polishing
- Laser welding is able to access areas that would be difficult to reach with other welding methods
The high quality and precise characteristics of Laser welding have made this process very beneficial in the following industries and applications:
- Aerospace Components
- Automotive Parts
- Food & Dairy Processing Equipment
- Medical & Pharmaceutical Devices and Equipment
- Electronics Components and Instruments
- Plastic Injection Molds
Resistance Welding
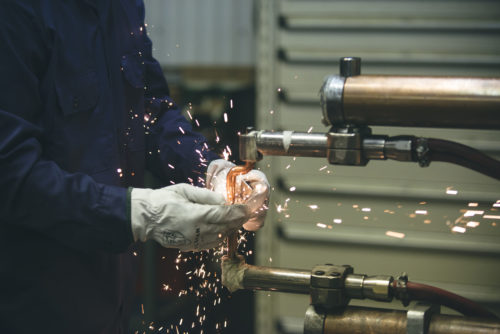
Resistance welding—also known as electric resistance welding (ERW)—uses pressure and electric resistance to produce welds. The resistance to the flow of electric current at the weld joint generates heat, which melts and fuses the materials together.
There are many forms of resistance welding, which differ in the characteristics of the welds they produce and the types of electrodes used to apply current and pressure. They include:
- Resistance spot welding: During resistance spot welding operations, a weld nugget is formed between two surfaces while they are held together between electrodes.
- Resistance seam welding: The resistance seam welding process is highly similar to the resistance spot welding process. However, it uses welding wheels to produce a series of overlapping nuggets along the weld joint rather than welding electrodes to produce a single nugget.
- Resistance projection welding: During resistance projection welding operations, electricity, force, and weld time are concentrated on raising projections across the weld surface.
- Resistance butt welding: The resistance butt welding process is used to join components with similar cross-sections across the entire joint surface rather than small areas.
- Flash butt welding: Flash butt welding primarily uses the resistance heat generated by the components and pressure to form a welded joint.
The main advantages of resistance welding are:
- Broad material versatility: Resistance welding can be used to join similar and dissimilar metals.
- Good cost-effectiveness: Resistance welding eliminates the need for filler metal, flux, and shielding gases, making it more cost-effective than other welding techniques.
- High efficiency: Resistance welding is extremely efficient, offering high welding and production rates. It can also be automated to achieve even better operational efficiency.
The resistance welding process’s low cost and high efficiency make it a preferred welding method for mass-production applications, including in the following industries:
- Aerospace
- Automotive
- General industrial
Robotic Welding
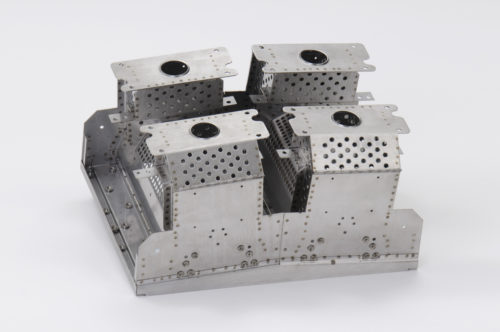
Robotic welding—also referred to as automated welding—uses programmable tools and industrial robots to partially or fully automate the welding process. From handling the part to performing the weld, the technology can be adapted to carry out various tasks with minimal human involvement. Automated welding systems can perform spot welding, arc welding, resistance welding, and other types of welding that are used in high-volume, repetitive operations.
When paired with the right applications, robotic welding provides the following benefits:
- Increased productivity and speed: Robotic welding setups streamline key operations in the welding process, allowing for faster turnaround and higher throughput.
- Enhanced safety: Robotic welding operations carry fewer operator safety risks, such as electric shock, arc glare, overspray, and exposure to toxic fumes.
- Improved quality and accuracy: Since each welding variable can be tightly controlled, robotic welding allows for repeatable welds with superior quality, consistency, and accuracy than those created using manual welding techniques. The increased accuracy and repeatability help reduce production costs by minimizing the need for expensive rework.
- Reduced labor: Robotic processes can be programmed to perform highly repetitive or laborious welding tasks, allowing manual welders to be assigned to more complex or customized welding operations.
Robotic welding supports high-volume, repetitive welding applications in a number of industries, including:
- Automotive
- Aerospace
- Electronics
- Production manufacturing
Welding Services at Lansco Manufacturing
Need a partner for your next welding requirements? Turn to the experts at Lansco Manufacturing! Whether you require MIG welding, TIG welding, resistance welding, or robotic welding services, we’ve got you covered. We also offer R&D support, prototyping assistance, and a range of other value-added services to ensure you receive finished parts and products that meet your exact technical specifications and quality standards. To learn more about our welding capabilities and other custom sheet metal fabrication services, contact us today. To discuss your project specs with one of our representatives, request a quote.